Problems that should be paid attention to during processing of difficult-to-machine materials
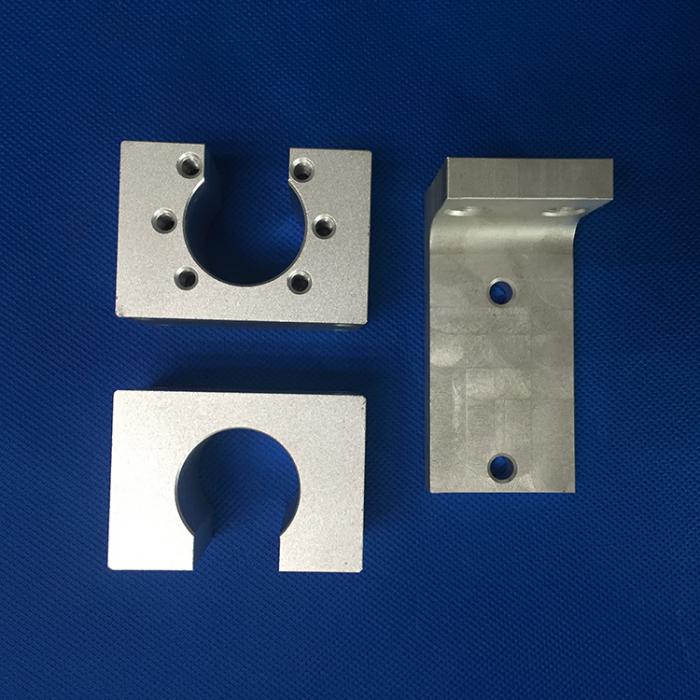
Machining is roughly divided into turning, milling, and cutting (end machining of end faces such as drills and end mills). The cutting heat of these cuttings has different effects on the cutting edge. Turning is a kind of continuous cutting. The cutting force of the cutting edge does not change significantly. The cutting heat acts continuously on the cutting edge. Milling is a kind of intermittent cutting. The cutting force acts intermittently on the cutting edge and will vibrate during cutting. The thermal influence of the blade tip alternates between heating during cutting and cooling during non-cutting, and the total amount of heat received is less than that during turning.
The heat of cutting during milling is an intermittent heating phenomenon, and the teeth are cooled when they are not cut, which will contribute to the extension of tool life. The tool used for milling is a ball end mill, and the turning is a general turning tool. The two are in the same material to be processed and the cutting conditions (due to the different cutting methods, the cutting depth, feed rate, cutting speed, etc. can only be roughly the same) The cutting comparison test under the same environmental conditions shows that the milling process is more advantageous for extending the tool life.
When cutting with a tool such as a drill with a center edge (ie, a cutting speed of 0 m/min) or a ball end mill, the life of the tool near the center edge is often low, but it is still stronger than that during turning. When cutting difficult-to-machine materials, the cutting edge is greatly affected by heat, which often reduces the tool life. If the cutting method is milling, the tool life will be relatively longer. However, difficult-to-machine materials cannot be milled from start to finish. There is always a need for turning or drilling in the middle. Therefore, corresponding technical measures should be taken for different cutting methods to improve processing efficiency.